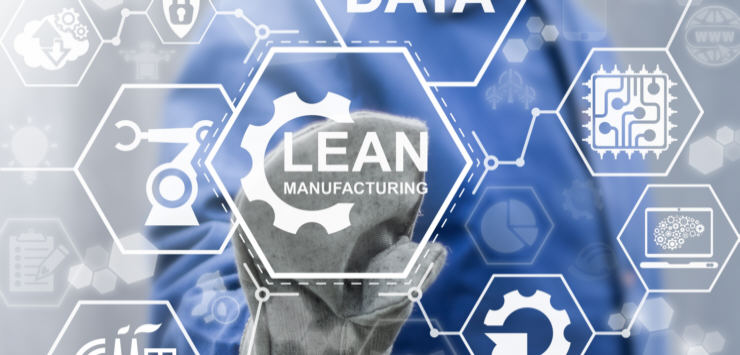
One of the most common statements you will hear in regards to implementing lean in a job shop environment is simply "It doesn't work here." Unfortunately in many organizations, this statement is true. If you try to apply lean tools the same way Toyota applies them, you probably will fail.
In my last position, every time a new manager, lean consultant, or continuous improvement engineer would come into the plant, the first thing they would do is try to draw a value stream map of the plant. I would tell them, "that's fine, you will have the state of the plant at 3:01pm, and by 7am tomorrow you will have to throw it away and do it again because the plant will be a different place by then." And it was. Soon they would realize what I learned through trial and error years ago, that a different approach was needed.
The reason for this is that job shops present their own unique set of operational challenges, which include:
- Most jobs are low volume and have a high degree of variation, never allowing the plant enough time to become truly efficient at them
- Many shops require engineering drawings and custom estimates for most products run
- Customers constantly interrupt production schedule by moving jobs, rush projects, and repair jobs
- Bottlenecks change on a daily basis according to the product mix
- Raw materials and outside vendors are difficult to coordinate to a constantly changing schedule
- Shop tooling, jigs, and workstations must constantly be moved as the product mix changes
- Many of the most popular lean and six sigma tools have limited effectiveness.
- Metrics are often difficult to formulate and track
You have to look at things from a different perspective. Stop trying to look for a cookie-cutter lean template, and start living the lean ideals instead. So I would revise the original statement in this article to "Lean doesn't work in job shops the way most people have been taught it." Here are some of the core elements to consider when implement lean in this challenging environment:
Continuous Improvement
Your business needs to focus less on the lean tools themselves, but instead gain a deeper understanding of the underling principles involved. Truly understand waste in your organization. Some work in progress (WIP) may be necessary to level-load constraints, but it needs to be managed and controlled. Transportation can be overwhelming because of all the movement of product between stations as routing changes constantly. Defects can quickly get out of hand if they are not aggressively addressed. Inventory can balloon if not carefully controlled.
There will also be a small number repetitive tasks in any job shop which can be optimized with standard lean tools. These opportunities are often overlooked because of the "lean won't work here" attitude.
Scheduling and Office Functions
If a lean schedule doesn't work, try taking a Theory of Constraints approach to your organization by identifying your bottlenecks, maximizing production through them, subordinating everything to those constraints, and eventually eliminating them. The scheduling process in the plants needs to focus on the plant's bottlenecks, level loading production around them, and adjust to the product mix and backlog accordingly.
Also, your whole operation, including sales, engineering, materials, quality, production, and transportation must be in alignment through a SIOP process. The plant cannot do it alone.
Don't forget to optimize the other functions in your plant front office either, as there are usually many opportunities due to the complexity of operations. Tasks like MRO ordering, approval processes, programming, and paperwork distribution all present opportunities for improvement.
Finally, your estimates and estimating process needs to be streamlined and accurate. Overestimating the hours required on a job will cause you to lose customers because of the higher price point. Underestimate your hours and you will fall behind on your schedule and potentially lose money that cannot be recovered because it is a one-time job.
Shop Floor
Rather than using complex value stream maps of the entire operation, narrow your focus by using process maps to optimize your operation at a low level, and then organize your plant layout to limit transportation waste between processes. Implement Smed and flexible work stations so you can rapidly adjust to changing product mix. Revamp your setup processes to do as much of it offline while equipment is running. You also need to have ample equipment and tools to allow flexibility and avoid waiting. The last thing you want is to have an entire department standing around waiting to use the one grinder in that area.
The flow of information on the shop floor is much more critical than in standard manufacturing. Engineering drawings need to be timely, accurate, and must be usable by shop floor workers. Priorities must be clear and well communicated. CNC programs must be efficient and available at the machines.
Raw materials and parts must be organized and delivered to the areas they are needed, when they are needed. Treat your different departments as if they are external suppliers, providing materials to the plant's core assembly and finishing customers. Work in progress needs to be limited to only that which is needed by your bottlenecks.
People
Usually your work force needs to be highly trained, including a huge degree of cross training to allow your plant the flexibility to adjust to your shop's mix. It is not uncommon to have a six month or longer period before a worker can truly be efficient, so you cannot skimp on training.
Standard work is a very powerful tool, but it needs to be implemented in an entirely different way. You should not have standard work for individual products, but rather processes. Those processes are then arraigned in different combinations to build your various products.
Quality
Quality control inspection needs to be optimized just like production processes as they face many of the same challenges.
Defects are easier to produce when you are always making something new, so don't be afraid to run quality Kaizens or Operational Excellence events to limit them in your processes.
Document your jobs well so you can learn from them and have a baseline for future jobs
Conclusion
This is just a sample of the steps you can take to optimize you job shop. Hopefully you will find articles presented here informative and that they help you on your lean journey.