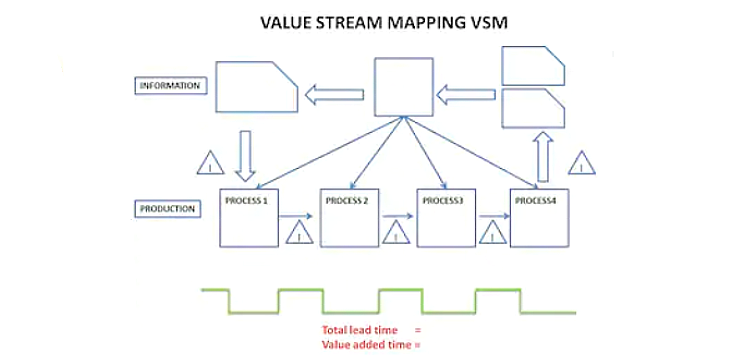
Value Stream Mapping, or Material and Information Flow Mapping as it is called at Toyota, is a powerful lean tool that graphically shows the flow of a product through a plant, and any potential wastes associated with the process. It also shows a future state scenario where these issues are corrected. If you are new to lean, I some good foundational reading is:
- Value Stream Management: Eight Steps to Planning, Mapping, and Sustaining Lean Improvements
- The Complete Lean Enterprise: Value Stream Mapping for Office and Services
Conventional wisdom states that Value Stream Mapping doesn't work in a job shop environment. On the surface, that is certainly true, it doesn't work the way it works in an assembly line operations. Our mix is variable, process times are inconsistent, and product does not always take the same path through the plant. In reality, you may not have one value stream, but 50, 500, or 5000. To make matters worse, you are running a mix of numerous products through your plant at the same time, so one map is completely incapable of describing what is going on in your operation. Swim lanes and other tools are often a better solution for job shops than value stream mapping, but even they are lacking in many areas.
However, like many of the other core lean tools, Value Stream Mapping concepts can be useful if applied in different ways:
Partial Maps
Don't feel obligated to do complete value stream maps. Doing a partial value stream map for a specific series of processes or products can provide valuable information. It may not provide the full picture like a traditional value stream map does, but you have to understand that no one tool will be able to provide that picture. You will have to piece together multiple tools do describe what is happening in your operation.
Plant Office Operations
While production on the shop floor varies significantly in a job shop, office operations are often very similar regardless of the work produced. Orders come in, drawings are produced, materials are ordered, work is scheduled, and jobs are scheduled and released. As such, office operations ARE an excellent place to implement Value Stream Mapping.
For example, years ago I implemented value stream mapping in the MRO ordering process of a plant, which was slow and very bloated. We build a value stream map, and upon careful examination determined that the problem lay with neither procurement nor maintenance, but in fact with other parties. All purchase orders were being routed through a plant controller and plant manager who had no idea at what he was looking at, and only cared about the total budget at the end of the month. These two were removed from the routing, but the production manager added in to verify the need for the maintenance procurements as they were much closer to the situation. The result was that lead time to order was cut by 70%.
This could be applied to nearly any office process with a linear flow, including drafting, procurement process, and HR on boarding.
Value Stream Mapping As Part of The SIOP Process
SIOP stands for Sales, Inventory, and Operations Planning, and is used to bring your organizations into alignment. It can also be used to greatly reduct the overall lead time for product, starting at with sales and ending with logistics delivering the product.
You can create a macro level value stream map as part of a value chain process. Completely ignore actual production time - simply block it out because it so variable - and focus on all the other steps in the process. For example, how long does it take to enter customer specs and to engineering? How long after engineering is complete to generate drawings? What is the lead times on various materials? How long does it take to secure trucks to deliver the product?
Engineered Products Lead Time Reduction
In some engineered products businesses, the products you are making are similar and take most of the same steps, but the process times vary immensely based on the product size or complexity. You can still use value stream mapping, simply ignore process times all together (treat them as variable), and focus on waste between processes in the lead time ladder, as shown below:

Map The Routes and Compare
If you are running many different products, focus on mapping each route a product can take through the plant, not each individual product. This will greatly reduce the amount of maps required. Like in the last example, ignore process times and focus solely on waiting. However, this time we will want to compare the lead time ladders at a specific processes, as shown below:
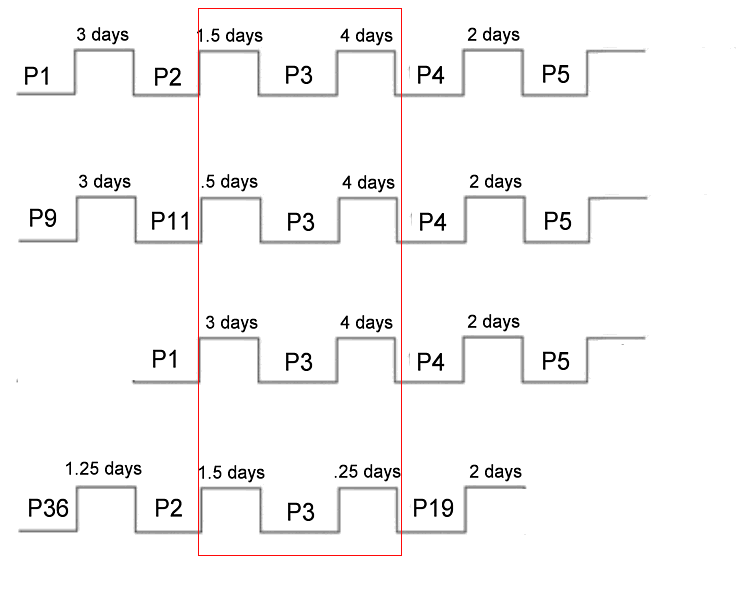
Looking at process 3, one should be asking why the wait time is lower when product comes from process 11, and why the wait time is less when routing product to process 19. Perhaps these can be replicated when using other routing.
If all the wait times were the same, regardless of the routings, this would indicate a constraint is present ala the Theory of Constraints, and would be a good candidate for lean events.
This technique won't work in all job shops, or even all the time in any shop, but you can pick and choose the situations and products you use it on and still get useful data from it.
Value Network Mapping
Value Network Mapping is a unique take on value stream mapping, where they use industrial engineering charting methods to create value stream maps that actually can describe a job shop somewhat accurately. While this topic is far too Below is a presentation on it:
Value Network Mapping from JobshopLean on Vimeo.
Conclusion
Value stream mapping is a lean tool that is often ignored in most job shops because of it's severe limitations, but it can provide useful data if we use learn when and where to apply it.