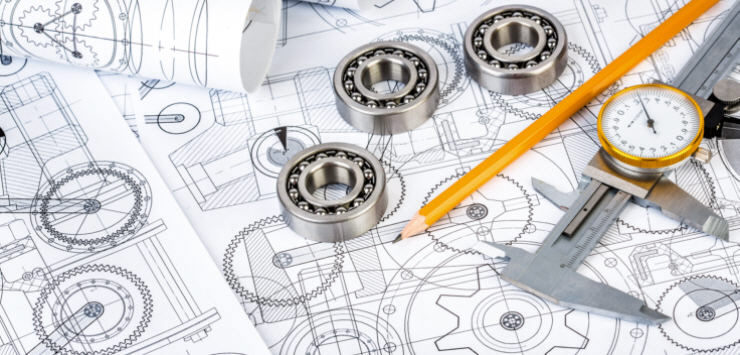
The flow and accuracy of information is critical in a job shop. This is magnified even further if you build an engineered product that is assembled via blueprints or technical drawings. Drawings need to not only be accurate, but also usable by shop floor employees and quality control to build the product. As a general rule, I tell any drafter or modeler that their drawings should be usable by someone with a 9th grade education, at 3am, in a dimly lit shop. If it's more complex or harder to read than that, simplify it. Below are key considerations and blueprint drawing considerations.
Design Rules
These rules are hardly a comprehensive list, but they will provide some food for thought:
- Use standard parts wherever possible. Simply because the product is custom engineered doesn't mean all the components need be.
- Modular designs are generally easier to assemble and inspect.
- Optimize between material usage and ease of assembly - saving $10 on material and then spending an extra $50 on labor is no savings at all.
- Be aware of potential shipping issues. When I was in the motorcycle industry, "apehanger" handlebars would only weight 3 lbs, but because of the dimensional weight standards from UPS and Fed Ex, they actually shipped as if they weighed 30 pounds. On the other end of the spectrum, large products over 10' wide or 80,000 pounds total truck weight need to ship over sized, which require special trailers, permits, escorts, and can add tens of thousands of extra expense to your product.
- Limit the number and sizes of fasteners used. Nothing slows down production faster than a large number of different sized fasteners.
- Make sure the finished product can be material handled, both within the shop and in transport.
General Drawing Rules
- If you want it on your product, it should be on your print. Period. I've heard of companies not wanting to put too much information on their prints for fear of competitors building their products for their customers. You are just shooting yourself in the food by doing this, and is the reason why there are lawyers.
- If you don't call out specifications on your prints, clearly reference where you do. You may also need to include a copy of those specifications with each drawing package. It is not reasonable nor advisable to have a floor employee going to look up an ASTM standards.
- Don't treat engineering drawings and manufacturing drawings as the same thing - they are not necessarily the same. For example, your may have one set of drawings to send your customer, and another set for those building them.
- Keep your part numbering systems consistent between prints and projects.
- Be consistent in how you dimension and view between drawings on the same product. Nothing is more confusing or frustrating than when this is changed mid-project.
Dimensions
- For anything that is assembled and measured with a tape measure, try dimensioning from one end, in increasing increments. Imagine a worker putting their tape on the end of the product, then walking the length of it marking out locations as they go. This is how it will be assembled.
- Don't give a center of hole to center of hole dimension, unless it is for a machining operation. How does one accurately measure to the center of a hole?
- Don't make the shop floor employees do math. At 3am, with a new employee with limited math skills, forcing them to add fractions is a recipe for disaster.
- For Forged parts, you may not be able to hold all the dimensions you want. If you have 3 critical dimensions, only two may be held in the forging process. For welding and some machining processes, excessive heat causes distortions which may require a great deal of extra rework on each part to hold your dimensions. Be aware of all these things in your designs.
Units of Measure
- If your people are measuring with a standard tape, don't put dimensions in 1/32" or less.
- Similarly, don't give measurements in ten thousands if your workers are only equipped with simple calibers capable of going to one thousands.
- Simply because a 33/64 drill bit is the closest conversion from a metric size doesn't mean that you should size the hole this way. If possible, size it to the next standard size up. You will reduce the tooling on hand required, and reduce possible delays.
Font
- Fonts should be simple, a readable sized text, and bold enough to be read in shop floor lighting. This is especially true with electrical schematics.
Verbiage
- Clean up sloppy dimensional wording (critical, standard, reference, minimum, approximate). For example, I have seen a dimension called at as 20" minimum. So is 6210" acceptable then? That is technically correct, but of course not what you were really looking for.
- Avoid use technical terms that your average slop floor worker will not understand.
- This should be obvious, but you should have drawings in the language your work force uses. Often prints will be made in English and Spanish, with the Spanish conversion in parenthesis after the English version.
Views
- Whenever there is a lot of clutter, you should provide an expanded view to aid the shop floor.
- As a general rule, "Notes" on drawings to be replaced with views.
- Give views from multiple directions in complex drawings. 3D views are even better yet if your software supports it.
Efficiency
- For machined parts, be aware that the time it take to load and unload the machine is money flowing out the door. Also, try to design parts that can be machined in a limited number of passes, and with a minimum of tool changes and movement.
- For Welded parts, keep in mind that the welder has to be able to get into position to weld the parts. Extremely tight spaces and angles make it nearly impossible to get a good weld. This is compounded for structural member which may require a full penetration weld and need to be tested.
- For assembled products, you may wish to consult with the shop floor during the drafting process to ensure the products can actually be assembled as rendered.
Materials
- Weld symbols should be on drawings, especially for welds that need to be tested
- Materials used should be clearly called out, including any special grades required
- Not only should the finish be called out, but any primers required. For example, when painting over galvanizing a wash primer may be required, and should be called out on prints and bills of material
- Hardware sizes, threads, and grades needs to be called out in the correct quantities on prints and in the bills of material