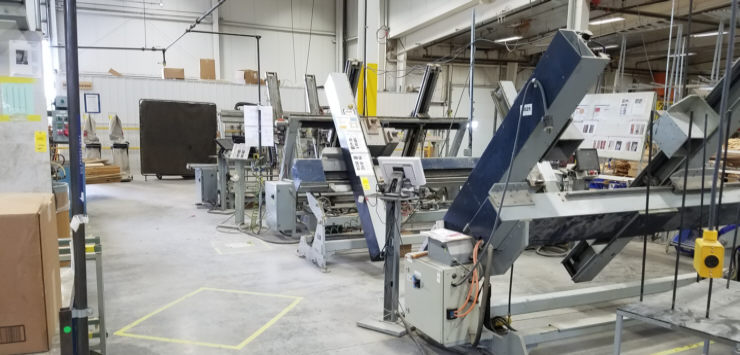
So you may be asking yourself, do I really need to calculate my capacity down the the process or even the machine level? If your work backlog is measured in hours, the short answer for most job shops is yes.
Jobs shops have a mix of different jobs flowing through their plant at one time, often with unique routings and process times. This mix leads to the creation of moving constraints throughout your operation which need to be identified and managed. It also leads to losses in efficiency in processes that have more capacity than work, so workers slow down to make what work they have last. In these starved processes we can also create unneeded WIP when we pull up future scheduled jobs to "keep them busy", and then these parts sit around collecting dust until the processes that need them catch up. Mapping your capacity in hours at each process or work cell can help identify and minimize these issues.
If you have not already done so, please check out our article on overall plant capacity planning as it is the foundation for much of what we talk about here.
Getting Started
So lets get started calculating capacity at the process level. At it's simplest level the capacity of a process is the product of hours worked each day, work days in the month, and number of stations available in the process. If we calculate it on a monthly basis:
Hrs available/day x Work Stations x Work Days/Month = Process Capacity
However, there are a number of factors that reduce the hours available each day, which we detail in the next sections.
Process availability
In most plants all processes are available all the time, so this is a non-factor. However, if you have process that can only be run some of the time, this needs to be factored in. For example, I know of company that has outside crane work that can only be done during daylight hours because of safety, even though they run 24-7. They cannot have substantial outdoor lighting for night work as they are at the end of airport runway and they FAA will not allow it. The hours of available also increase in summer and decrease in winter along with the daylight hours.
Setup, Change-over, and Non Value Added Times
Set up times need to be considered if you have short process run times, are running a lot of small jobs, and constantly need to change tooling or reconfigure for the next job. It can also include time to removal scrap (like on a cutting table), material handling in and out of the station, or re-configuring the work cell. These are process steps that do not add value (change the fit, form, or function) to the product, but are required to complete the process. You should not include times of functions that can be done while a machine is running.
You probably will have to do some time studies to see how long it actually takes to handle these operations. For most operations it is enough to take simple average of the number change overs required per day and the average time per setup. For complex processes with varying setup times can create product or process classes where you group together similar product/process setup times, and track them separately.
Many managers and lean engineers cringe at thought including a waste time in your capacities and ultimately your schedule, but you absolutely have to consider it. Our goal here is to create an accurate "current state of available time" for the process, not to indulge in wishful thinking that creates constraints and negatively effects on-time delivery. These are opportunities for improvement, and once this waste is removed for the process, then it can be removed from the capacity calculation.
Maintenance
The biggest consideration here is preventative maintenance on machines. If the machine has a one-shift long PM scheduled each month, those hours need to be subtracted from your monthly total. Likewise, if operators have 10 minutes of PM's that need to be done at the start of each shift, this time needs to be taken out of your capacity.
If you have a very good total productive maintenance program in place, know what your OEE score is for a piece of equipment, and have a machine that averages a lot of downtime, you may wish to subtract the average downtime from your capacity as well. Again, this won't be popular with certain members of your organization. Don't pretend the downtime doesn't exist - fix the problem - then remove it from your calculations.
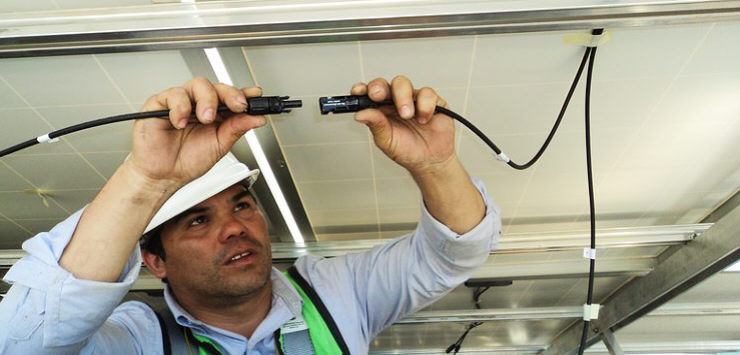
Other Machines With Lower Efficiency
It is not uncommon for a manufacturer purchase a large new piece of automated equipment, but keep the old equipment on or offline as either backup or overflow capacity. You may also have multi-use equipment that can also do the work if needed. The reason this other equipment is not always used is usually because of lower efficiency, but we should still include it for process capacity.
Here is how I handle this situation: Base your process capacity on the best machine, and then add to that capacity these "backup" machines adjusted for efficiency. For example, if I have a new CNC lathe with 7 hours capacity, but I also have an old manual lathe in that department that can do the work but is only 50% as efficient a process as the CNC machine, I use the following equation:
Process capacity/shift = CNC machine capacity + Old Machine Capacity
10.5 hours/shift = 7 hours + 3.5 hours
Similarly, you could also calculate your "machine equivalents":
Process Machines = Full Capacity Machines + (Partial Capacity Machines x Efficiency)
1.5 = 1 Full Capacity Machine + .5 Partial Capacity Machines
I base the time off the CNC machine because that is the normal machine that would do the work, and we don't want to overstate our capacity by assuming the old machine would run at that same efficiency.
Dual Use Machines
Another common scenario in a job shop is the following:
I have 4 machines, 3 of which have identical specifications and can do 20" product, but the final machine is much larger and can handle 30" product.
Even though these are all technically the same process, you should separate this larger machine out into it's own process for capacity purposes. The problem occurs because there is overlap the processes, where the large machine can do all work, but is only the large machine can handle 20"-30". This can be handled easily if you have a good software package, simply set an "OR" conditional statement for the capacity that will look something like this:
All product under 20"
Hour capacity per machine = 7 hours/shift
Capacity = 28 hours/shiftOR
Mixed product ranging up to 30"
Hour capacity per machine = 7 hours/shift
< 20" Capacity = 21 hours/shift
20" to 30" Capacity = 7 hours/shift
Alternatively, you can handle the situation by including the large machines capacity in both the under 20" and 30" categories, then flagging any work coming in over 20" and manually removing those hours from the 20" capacity. There is no right answer here, just whatever works best in your organization.
Labor Hours Earned Per Shift
The last component we need to look it is the number of hours your workers earn (on average) per shift. You can not produce product if no one is running the machine or building the product.
I detail the process of calculating the number of hours you earn per shift in my Capacity Planning article. Basically we are going to take the hours available in a shift, and subtract time the average time for meetings and breaks.
Summary
Let's do a short example to tie everything together:
On average, you earn 7 hours for every 8 hour shift you work. You have a process that has 3 work stations, and you have an old machine in the corner that you can run this process on at 50% efficiency. You run a 5 day a week, 24 hour per day operation and there are no times that this process cannot by done. On average setup times account for .5 hours per shift for each work station. You have two preventative maintenance tasks that are done on each of the work stations in this process each month, and if you average the time about .25 hours of per shift used. There are 21 work days this month.
First, if we calculate hour many hours we can earn at each work station, we have:
Hours Earned per Shift (avg) - Setup - Maintenance = Hours per Work Station
7 - .5 - .25 = 6.25 hours
Next, let's calculate work station equivalents:
Work stations running at 100% efficiency = 3
Work stations running at 50% efficiency = .5
3 + .5 = 3.5 work stations
Finally, let's bring it all together in our original equation:
Hrs available/day x Work Stations x Work Days/Month = Process Capacity(6.25 hours x 3 shifts) x 3.5 work station x 21 days = 1378.13 hours capacity
Next Step
Once you calculate all your process capacities, you can then apply the tools described in the articles below to improve your schedule, reduce WIP, and improve your efficiency: