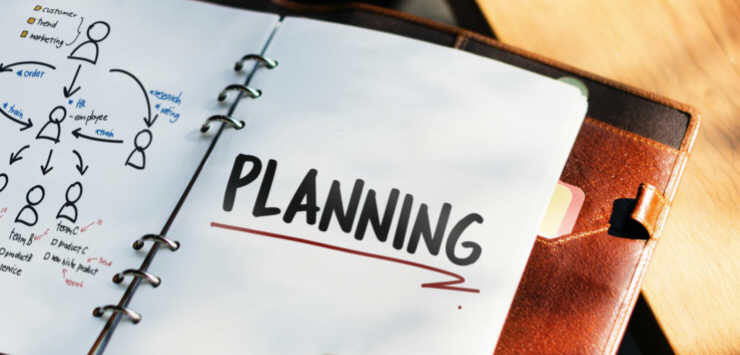
Most job shops are essentially selling time. Whether it's hours of machine time, hours of skilled labor, or both, capacity planning for most of us boils down to how many hours we have available in our operations.
The problem is many companies are bad at it, and this issue not just confined to small operations. I know a number of plant managers and vice presidents in fortune 500 companies are unemployed because they didn't get capacity right. For example:
- One firm allotted the same number of hours capacity each month. As I'm sure you've noticed not every month has the same number of working days. Also, they apparently didn't take into account that these plants were closed for holidays.
- Another manufacturing company assumed each employee earned 8 hours in an 8 hours shift, and that they always worked at 100% efficiency. This is actually a pretty common mistake, and needless to say they were perpetually behind and worked a lot of overtime.
Thankfully, I have a simple step-by-step process and excel calculator tool to get you on the right track. The process detailed is for the overall plant capacity. You may also find it beneficial to calculate your capacities down to the process or machine level, which we detail in our article Capacity Planning at the Process Level.
1) Staffing and Capacity Planning
The first thing you need to do is review your direct labor staffing in each department, on each shift. Do not include indirect labor such as maintenance or material handlers, only people who can earn an hour of labor on jobs. You should have this available in a staffing plan.Once you have these numbers, you have a few potential obstacles to deal with:
How do you handle working leads?
In some manufacturing operations, leads fill a supervisory type role and are strictly indirect. In some plants, however, the leads are "working leads", and a part of their time is spent doing production work, and part of their time is spent setting up the department.
If your leads fall in the latter group, you will have to calculate what percentage of their time is spent on production work, and modify accordingly. For Example:
If you have 10 leads, who spend 45% of their time on production work, you should only could 4.5 towards your capacity (10 leads x .45 = 4.5)
Adjust for Workers in Training
Workers in training should NOT be counted as a full employee for purposes of capacity, particularly in job shops. Often our workers fall under the "skilled craftsman" category and take significantly longer to work at full efficiency. In fact, new hires are often a drain on efficiency as we have them training under our "star" veteran employees, which dilutes their efforts on a daily basis as well.
There are several different ways to handle this.
First, you can simply set an arbitrary date, and after which you count them towards capacity. Often this is the date they are no longer in their probationary period.
The other option is incrementally add them to capacity. This works well for operations with a long training period. For example, at my last company we assumed it took employees 6 months to fully get up to speed. So we did not count them at all under 2 months, took 50% their hours at 4 months, and counted all their hours at 6 month.
2) How Many Hours Can Be Earned?
This part of the capacity planning process trips a lot of companies up. So just how many hours can your workers earn in an 8 hour shift?
Surprisingly, the number is often very low, around 6.8 hours per shift/worker for most operations. What was the formula I used to come up with this number?
- Number of breaks x minutes on each break (2 x 15 minutes = 30 minutes)
- Toolbox talk meeting to start the shift (10 minutes )
- Shift Changeover/clean up at the end of the shift (10 minutes)
- Average amount each day spent in meetings. They have an hour safety meeting and general information meeting each week, that's (120 minutes/5 = 24 minutes each day)
So around 74 minutes a day they are not earning hours, which roughly translates into 406 minutes, or 6.8 hours a shift that they are earning hours.
Think this number is too low? Think again, if anything it is probably too high for most organizations. I wrote another article that explores the lost time in meetings in more detail called Meetings: The Ninth Waste.
3) The Effect of Absenteeism on Capacity
This one is pretty simple. Have your plant controller or HR tell you what the average absenteeism rate is each day from ALL sources, including vacation, FMLA, leave of absence, sick days, and reported.
We will multiply this by our daily total later on. So if we have 10% absenteeism, we will multiply the hours available by .9.
4) Efficiency
Efficiency can be a little tricky due to corporate politics. Some organizations won't let their manufacturing plant schedule for anything less than 100% efficiency. Any short comings are expected to be made up as overtime.
I don't feel this is a realistic expectation unless your average plant efficiency is near 100% already, but that is the way it works sometimes. Even if the organization you report to won't let you modify your capacity for efficiency, you need to know this number anyway so you can plan accordingly.
Just like absenteeism, it is a simple multiplier of the total hours each day.
5) Maintenance Issues
This one is an even harder sell than efficiency. If your machine up-time or OEE (Overall Equipment Effectiveness - wiki) is terrible, you may wish to include a simple modifier to your overall hours.
I'm not going to go into much detail on this as most organizations will not allow you to add this to capacity. Simply be aware it is out there and does effect your schedule.
6) Number of Work Days
The first part of this is simple, each month has a different number of work days, simply count the number of work days available for each month, subtracting any holidays the plant is closed. Easy enough.
But we need to dig a little deeper as there are other factors that come into play as well. Examples Include:
I worked in a union facility that allowed unlimited number of people to take vacation the day before and the day after a holiday. As a result, we only earned about 50% of our normal hours those days, so for capacity purposes we only counted those as 1/2 days. I also worked for clients in Southeast Asia that during the rainy season they shut down the plant on average 2 days as the roads were impassible. What if you're shutting down the plant for 3 days for machine upgrades? Account for those days or partial days as well. The end of the year posses a special situation as well. Many businesses are closed for the holidays, so you may not be able to deliver past the 3rd week. One way to handle this is to roll over any production from December into January. So for example, December may end up being a 15 day month for purposes of capacity this year, and January of the next year may end up being a 28 day month.
Each business and manufacturing location is different, so it is important to understand the special circumstances that could effect your work days.
Final Calculations Example
Now it's time to calculate our totals, and to introduce an excel tool to do it for you. Let's run through an example:
So let's say you run a plant that has 3 direct labor departments, with 20 people in each department, over 3 shifts (180 total). Each department has one working lead, that spends 50% of their time doing production work. You also have 1 person in each department on each shift in training that you only consider 1/3 efficient. Your plant controller has calculated that each worker earns, on average, 6.7 hours each day.
Your plant absenteeism is 15%, your plant efficiency is 90%, and you don't consider maintenance to be a major issue.
You have been tasked with planning your overall plant capacity by hours for next month.
Formula:
3 departments x 20 people x 3 shifts = 180 direct labor worker shifts
+
3 departments x 2 leads x 3 shifts x .5 (50% of time working) = 9 Lead shifts
+
3 departments x 1 trainees x 3 shifts x .333 = 3 trainee shiftsTotal number of direct labor shifts that can be earned each day = 192
192 shifts x 6.7 hours that can be earned x .85 absenteeism x .9 efficiency = 984 hours that can be earned each day.
Next month has 20 working days, with no holidays or special conditions.
Your plant can earn 20 days x 984 hours = 19,682 hours next month.
Excel Capacity Calculator
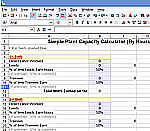
Don't worry, I wouldn't think of wrapping this article up without a tool to help. Below is a simple Excel spreadsheet to calculate overall plant capacity. Download it, modify it, and use it any way you see fit.
CAPACITY PLANNING EXCEL CALCULATORConclusions
The capacity I presented here is a very simple, watered down overall plant capacity. In our SIOP article we talk in more depth about addition factors that effect plant capacity.
Also note that you should calculate by work cell or department, and not just use overall employees. Often you will find that you not only need to calculate overall capacity of your plant, but you will need to know the capacity of each department as well to help manage your bottlenecks.
Capacity is a critical number of the operation of your business, and will act as one of the baselines for lean and continuous improvement activities over time. It needs to be accurate, and should NEVER include anticipated gains from Kaizen events or equipment purchases. This is not the time to be brave. Get those systems running, and recalculate it after changes are in place.
Also, your organization might require you to report a higher number (regardless if accurate) for political reasons or to give you "Stretch" goals. An accurate capacity is crucial for you as well so that you can determine the delta between performance expected and current state.