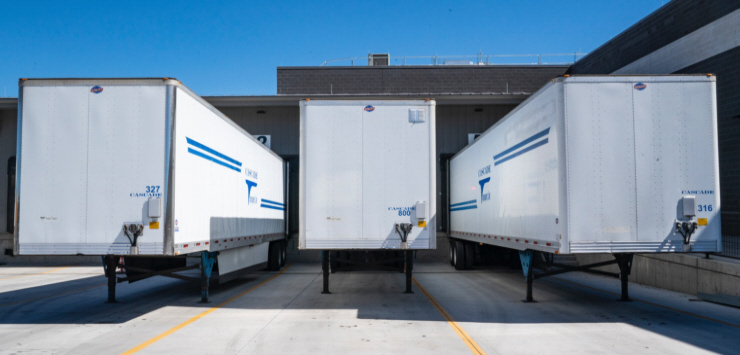
Background
In continuous or large batch operations, work flows through a set route through the plant. Process times are generally consistent with each piece of product that flows through the system. Constraints are generally easy to spot as they occur where large piles of Work in Progress (WIP) accumulate.
One of the common denominators in most job shops is that work doesn't always follow the same routing, and process times are rarely consistent between jobs. These issues are magnified by the fact that batch sizes are generally very small, and there is a mix of these various jobs and routing. Work in Progress (WIP) tends to be everywhere even in the best of times. Constraints move as the product mix changes.
As your constraints move throughout your shop, something interesting can happen. They stop being constraints in the classical sense. In a one piece flow or continuous operations, constraints limit the throughput of operations after the constraint. But in job shops, it is very common to have a large amount of work available after a constraint because other jobs are following a different path and their parts may skip over the constraint area. When the parts from the constraint area are finished, they are simply added to the queue of parts in the next process in a different order than planned. So in effect, the constraint hasn't limited throughput, but it has pushed back your schedule, added lead time to the production, and possibly caused a late delivery.
Let's look at a graphic example. Below is a diagram we used to describe constraints in our bottlenecks article. Water flows through the system, is constrained at process 3, and limits the throughput of the system.
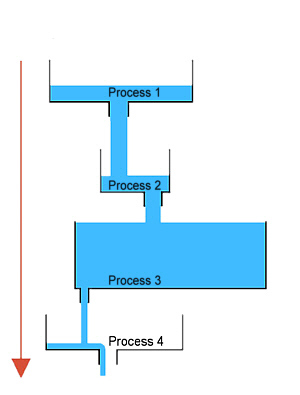
In a Job Shop, the system and constraints are often much more complex, and as you can see in the diagram below, water has multiple paths to flow. In this case, water isn't constrained, but it does take longer to get through the system. And keep in mind, this diagram is only accurate for one point in time; much like a Value Stream Map, it will change as soon as your mix changes.
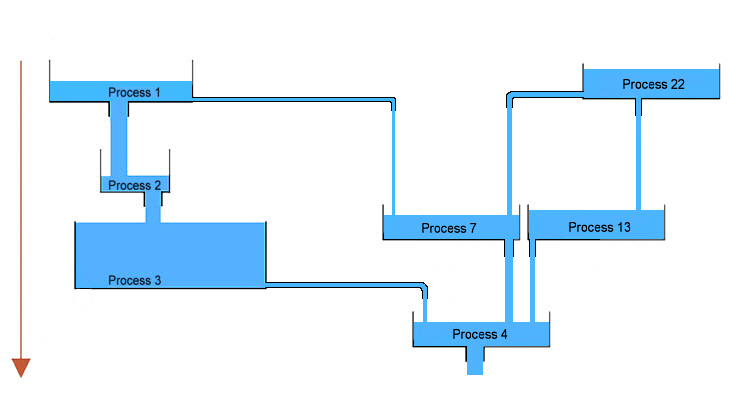
In this example, even though water is still constrained in process 3, process 4 still has plenty of water due to supply from processes 7 and 13. And while some may think this is an extreme sample, it is not. If fact, it understates the complexity found in many custom operations.
Finding Lead Time Constraints
The process to find these constraints is relatively simple if you have the right tools. The simplest method is to dig into all your customer delivery misses and find what the common denominators is. Often you will find they all contained a process or series of processes that were the culprit. This is, however, very reactive and might not be the best way to run your business long-term.
A more proactive method is to develop a production tracking system that lists each process in your plant and if parts were ontime or late at each step, preferably with real-time data if possible. Your processes that go consistently "red" when the process before it was "green" will be where the constraints are at.Should I Address These In My Business?
At this point, a common question is "Do I need to address these constraints?" It really depends on your business model and customer expectations. It also depends if this is a one-off product that you don't anticipate running again, or a reoccurring problem. Obviously on the one-off product you may simply wish to document the incident and write it off as a lesson learned.
If you offer on-demand custom work where the clock is ticking, you absolutely have to address these constraints. Lead time is what separates you from your competitors, and extra hours or even minutes can be the difference between keeping or losing work.
In the engineered product world, you may or may not have to. You may simply be able adjust the schedule to a longer lead time and your customer may be fine with a little extra time. Keep in mind, however, that even in the engineered product world lead time is becoming more critical each day too, so it may be in your best interest to stay proactive.
Keep in mind that Lead Time Constraints can become full fledged throughput constraints if your mix becomes unbalanced and you get a lot of work running through the process over a long enough period of time. Work from other routings will not be able to make up the difference, and efficiency and plant throughput will suffer. So for most businesses it is best to address them as soon as possible.
How Do I Eliminate Them?
Unlike regular moving constraints, lead time constraints often can't be "scheduled out" like I discussed in my article Heijunka - Heijunka: Leveling Your Job Shop Schedule By Controlling Mix and Constraints. All you will do is add more lead time to the project, which is exactly what we don't need.
You will actually have to dig in and elevate and eventually eliminate these constraints as outlined in the Theory of Constraints process. It is as this level that you apply your lean tools. Do time studies and events to find the waste in the area. Start a TPM and 5S program, and apply them to these areas first. Develop single minute exchange of dies SMED processes and flexible work cells to increase the speed with which you change between jobs. Redefine the process to limit the amount of work it does, minimize material handling, and create standard work for it. This where the rubber meets the road so to speak, and where you apply conventional lean tools to your job shop.
Conclusions
Lead time constraints are unique to job shops and are created by the chaotic routings and process times present. They are often hidden from view by our product mix, and show up as late deliveries to customers.