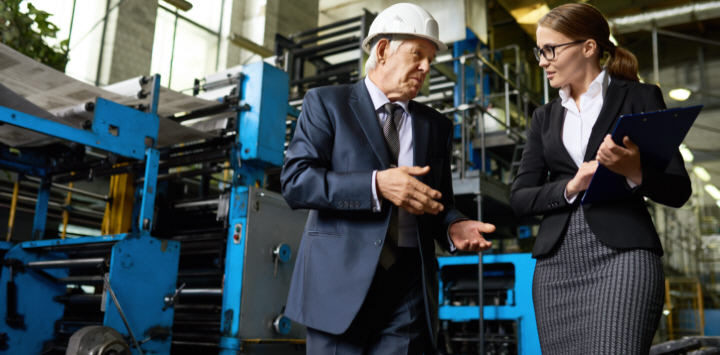
Open any book dealing with lean manufacturing, and one of the first topics mentioned is the Gemba walk, and how useful it is in installing a lean culture in your organization. It will talk about the management team seeing the product being manufactured, engaging the workers, and solving the problems they observed on the shop floor. But is this what really happens during a Gemba walk in most job shops?
Current State
Gemba (or sometimes genba) is a Japanese word for "The Real Place", and is generally accepted to mean "The Place Where Real Work Happens" in lean circles. In theory, the purpose of a Gemba walk is for managers to be able to answer this question: "Is the factory working as I think or assume it is working?" It should involve all management at some level as everyone in a plant environment has a direct stake in the success of the business. It should also involve the people on the floor so they can explain what is happening and what issues are limiting them. Finally the Gemba walk needs look at the process in general for correct information, proper materials, properly functioning equipment, and methods of doing tasks.
Unfortunately, that is not what actually happens in many plants. It is often a per-rehearsed route that involves a bunch of expensive office personnel standing in front of boards at various locations throughout the plant with very little interaction with the rest of the plant. The staff will walk from station to station, reading production stats or comments off visual boards. Even worse, they are often putting up notices or posting information for the shop floor, as opposed to getting information from it.
From the staff's perspective, there is very little interest as the walk is the same every day and generally only covers a hand of topics, most of which are not in their area or control, or were already known to participants prior to the walk. The key stakeholders, such as area supervisors or the production manager, already knew about any production or maintenance issues presented on the boards hours before. There is limited emphasis on areas such as materials or quality, and almost none on HR or accounting. Workers generally bring critical issues to their supervisors, and write suggestions on the boards that can frivolous in nature, or sometimes even confrontational.
The workers on the shop floor are not truly being engaged during the walks. Oh sure, a lead man will be brought up to discuss area issues, but generally they've already discussed those issues with their leadership. They are often in a hurry to get back to their "normal" jobs and feel the whole process is a waste as their time. Many of the issues they bring up are not addressed or the results not communicated. A large percentage of the shop floor workers are intimidated by the walk and to avoid it at all costs. In multi-shift operations, Gemba walks are infrequently done on the off-shifts, if at all, leaving a large part of your workforce out of the process.
There is also very little time spent actually watching processes, and almost no time spent in areas without boards. It's generally a race to get the walk down so the staff can get back to their work.
Do all of these apply to your walks? Probably not, but I'll bet some of them do. In Job Shops, the Gemba Walks SHOULD be even more valuable than conventional manufacturing as the current state and mix changes often, but sadly that is not usually the case.
Future State
So how do you change this dynamic? Here are some ideas:
Different Walk Each Day
There is absolutely no reason to walk the same route each day in a job shop. In assembly line manufacturing it is valuable to walk the value stream in reverse to see where bottlenecks are. In job shops, your bottlenecks change each day, so why should your walk remain the same? Follow your bottlenecks and focus your attention on adjusting to them. It can also be useful to follow the path your product is taking that day - it can be quite an eye opening experience when you see all the transportation wastes occurring in your plant.
Multiple Walks Each Day
While you may only have one "official" walk, your staff should be walking the shop floor. As a production manager I did at least one walk each shift, and usually many more. Your safety, quality, maintenance, and possibly materials managers should be doing the same. The Gemba walk is not meant to replace normal manager interactions with the shop floor, but as a structured event to augment them.
Focused Approach
Your "official" Gemba walk(s) should be focused with a specific topic in mind. It could be a critical KPI the plant is missing, or a near miss in safety. I prefer to actually have a rotating schedule where each functional area picks a topic for their walks. For example, when materials controls the walk, you may want to walk out into a receiving area to see the state raw materials are coming off of trucks. Quality may want to focus on scrap off a particular machine, while safety may want to focus on a process that had a injury or near miss. You still need to be aware of everything going on the plant from a safety, quality, cost, and delivery perspective, but focusing on a main topic provides structure and ultimately better results.
Staff Leadership
This one goes along with the focused approached. Your staff should not be participants in these walks, but should be leading the ones that are related to their area of control. The production manager should be leading a walk on efficiency, quality manager leading one on rework, and so on. Leading the walks forces your staff to engage in the process, think about your flow at a deeper level, and prevent them from simply going through the motions.
Involve Only Those Who Need To Be Involved
One common mistake is to have your entire staff on each walk; don't. There really is no good reason for it. Involve only those that need to be on that walk, and if a problem is observed affecting them, bring them in for the problem solving phase. Too often I see plant controllers and HR generalists walking around shop floor completely disenfranchised with the process because it is a waste of their time. The only staff members who need to be on every walk are your production manager and plant manager as they are only ones involved with safety, quality, cost, and delivery.
Schedule Time To Do Audits of Processes
Each walk should have a short period of time, 5-15 minutes, dedicated to actually stopping and watching a process. Conduct it as you would a time study - simply take notes and observe.
Checklist
The leader of each walk should have a checklist of stops and topics for each walk. This will increase the efficiency of the walk and reduce dead time.
Feedback
Nothing drives a shop floor worker to apathy faster than having their suggestions ignored. All suggestions or comments on boards (or in person) need to be addressed in a timely manner, and those need to be communicated back to that person as soon as possible. Give a time frame you expect completion, and who is in charge of the action. Even if you do not plan to take action on an item, you still need to communicate back to the worker with reasons why.
Stop Making Your Gemba Walk "A Boss Walk"
The Gemba walk itself should be about observing, and not discipline. That's not to say that you won't follow up on issues you see on the shop floor, but do it offline if possible. Obvious exceptions to this are safety, quality, or HR issues which must be addressed immediately.
Stop Trying To Solve Problems
Much like the previous comment, the Gemba Walk is about observing and learning about the problems, not solving all of them on the spot. Simple problems such a missing paperwork can be addressed immediately. With more complex problems we are often jump to rash judgments and solutions before we understand the entire problem. These problems will require more advanced problem solving tools to properly find the root cause. Finish the walk, then work on solving the problems in the post meeting, or as an assignment.
Engage your people
Stop and talk to your people on the shop floor in impromptu scenarios. If you see someone struggling or working on a very complex product, stop and talk to them about what they are experiencing. Do not judge and simply listen to what they have to say. You will learn more in a 2 minute conversation like this with your workers than you will in a month of scripted walks. After a while your workers will begin to seek your team out on walks if you handle this properly.
Pre and Post Walk Meetings
You should have a board in your office dedicated to your Gemba Walk. Meet at the board on-time, and have the leader give an overview of the topic and route. Once the walk is completed, have a post walk meeting to discuss your findings. You should also have a schedule posted of the days each functional area is responsible for the walk.
Action Tracking
You should have a system in place to track the actions that need to be taken, who is responsible for them, and when they need to be done. Review these action periodically, and senior plant leadership needs to hold their staff responsible for completing them in a timely manner.
Sample Walk Schedule Template
The actual walk itself is going to be dictated by the needs of your plant. Below is an example template of how you can schedule walks around functional areas, and some possible topics.
Area: | Production |
Leader: | Production Manager |
Core Participants: | Plant Manager |
Additional Participants: | Scheduler, Continuous Improvement Manager, Maintenance Manager |
Frequency: | 2 days a week |
This walk will change as dictated by mix and issues, and could include topics such as on-time delivery, efficiency, lean opportunities, and waste. The walk may also include watching potential bottleneck areas. |
Area: | Safety |
Leader: | Safety Manager |
Core Participants: | Plant Manger, Production Manager, Maintenance Manager |
Additional Participants: | Continuous Improvement Manager |
Frequency: | 1 day a week |
This is the perfect opportunity to do a Job Safety Observation. Other possible topics could include having employees walk you through a near miss, or getting feedback on potential hazards. |
Area: | Quality |
Leader: | Quality Manager |
Core Participants: | Plant Manager, Production Manager |
Additional Participants: | Continuous Improvement Manager |
Frequency: | 1 day a week |
The quality walk will examine finished product to visually inspect overall quality, to watch the process as it is occurring for compliance with quality procedures, six sigma control charts, and talk with inspectors/workers on the floor. The walk could also focus on a problem area, such as a machine with high scrap rates, or customer escapes. |
Area: | Materials |
Leader: | Materials Manager |
Core Participants: | Plant Manager, Production manager, Quality Manager |
Additional Participants: | Continuous Improvement Manager, Purchasing |
Frequency: | 1 day a month |
The focus of this walk will be to look at material that has come in, talk with material handlers and receiving, and talk with operators that initially process raw materials for feedback and issues. |
Area: | HR |
Leader: | HR Manager |
Core Participants: | Plant Manager, Production Manager, Maintenance Manager |
Additional Participants: | Additional Participants: Continuous Improvement Manager, Safety Manager |
Frequency: | 1 day a month |
The HR walk could should address access/usability issues, compliance such as required legal posters, inappropriate materials or behavior, state of bathrooms and locker rooms, and general employee welfare. |
Area: | |
Leader: | Maintenance Manager |
Core Participants: | Plant Manager, Production Manager |
Additional Participants: | Continuous Improvement Manager, Plant Controller |
Frequency: | 1 day a month |
The maintenance walk could focus on a variety of topics, ranging from problem machines, how workers are taking care of equipment, or capital expenditures needed. |
Area: | Accounting |
Leader: | Plant Controller |
Core Participants: | Plant Manager, Production Manager |
Additional Participants: | Continuous Improvement Manager, Materials Manager, Maintenance Manager |
Frequency: | 1 day a month |
The accounting portion could including ways to reduce plant overhead, inventory, WIP, and capital expenditures |
Conclusion
The Gemba walk is a valuable tool if you learn how to adapt it to your job shop environment. The key is to get your staff and shop floor engaged by making the exercise useful and efficient. If you have other ideas or suggestions, we'd love to hear them in the comments below.