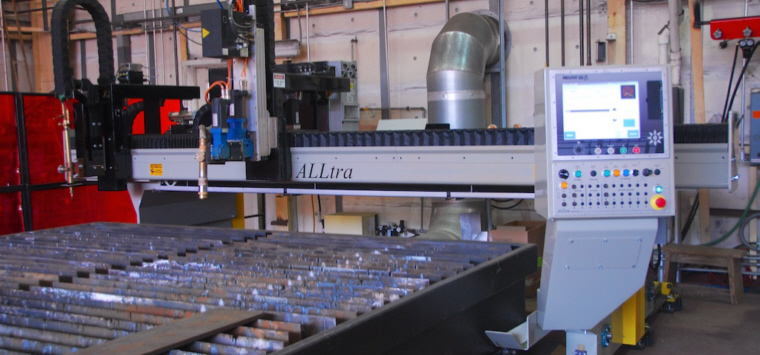
Our Case Studies series of articles are designed to highlight lean success stories in the hopes that you can find both inspiration and practical tips on doing the same in your shop floor. In some cases we will name companies and show actual pictures, in other cases the companies have chosen to remain anonymous and we will give descriptions and diagrams.
The Problem
A Northeast US manufacturer of custom-engineered steel products had a problem: their main plasma cutting table could not keep up with demand from both internal and external customers. The Alltra machine was only 2 years, in very good shape mechanically, and utilized new Hypertherm plasma units. Quality was just ok with very few parts needing to be scrapped, but some did require rework. The staff was veteran and hardworking, yet not matter how much overtime was worked, the machine and plant as a whole kept falling further behind. It was obvious to plant leadership that a new approach was needed.
Analysis
Many time studies were performed over a two week period to examine the process and supporting functions to look for opportunities. The company was a custom manufacturer where no two parts or products were the same, so it consuming to nail down all the critical data. Once they did, a some critical observations were observed:
The processes customer needed on average around 121 pieces cut per day (which represents 20 hours of WIP), but the plasma table could only provide 86 on average (again, 20 hours' worth). So the Takt time was:
Takt = 1200 minutes/121 parts = 9.9 minutes per part
However, the process could only supply a cut part every 13.9 minutes.
The table had to do all their own material handling, including using the gantry to bring in steel plate.
An average of 3 times a day the correct program was loaded into the computer.
It took an average of 19 minutes to change consumable for the plasma torches. Consumables needed to be changed when the jobs jumped to thicker plate, and when they wore out. Consumables were not available at the machine, they had no place to assemble them, and tools were stored in a buck by the machine.
Even though the machine had multiple water tables, the operator cut scrap and removed finished product with magnets while the machine was idle.
Solutions
A team of operators, supervisors, and senior management was formed to develop solutions. A series of Kaizen events were held, and the following solutions were implemented.
A Drum-Buffer-Rope
The machine was often starved for both plate and programs, so a drum buffer rope system for both was installed before the machine.Material handlers for the outside plate yard took over duties of bringing plate to the machine to free up the machine helper.
A buffer of 8 hours worth of work was placed in front of the machine that was monitored by the material handlers.
A buffer of 48 hours worth of programs was placed on the network of the machine as no programmers worked on weekends and the machine was on a 24-7 schedule
5S
The machine's consumable area and tools underwent a complete 5S transformation.A lighted table was build next to the machine, and all the tools needed were placed on a shadow board.
A small shadow board was placed on the machine itself near the plasma heads that contained all the tools needed to disassemble them to change consumables.
The vendor that supplied consumables put in and managed a vending machine right next to the table that had all the PPE, consumables, and other tools like grinding disks that might be needed at the machine.
SMED and Standard Work
Both SMED and Standard Work was utilized to increase arc-on time of the machine by moving tasks that were not value added into the machine run time.The consumable changeover process was completely revamped. A series of holders were placed on the consumable table that allowed a set of consumables to be assembled and readied offline. A set of gauges was purchased to measure consumable wear so they could be changed out before they produced bad quality cuts that required rework. The consumables were also changed out to a premium version with longer wear life.
The product and scrap removal process were revamped. Standard work was put in place so that a plate was always setup to run on the next table. As soon as work was complete on one sheet, the gantry was moved to the next sheet, the alignment checks were done, and cutting was started.
While the machine cut, scrap and product was removed from the table. Standard work for how scrap was to be cut up and removed was develop, as well as the most efficient way to remove product.
Organization and Visual Workplace
Area was market off in front of the machine to mark the buffer area for raw material. When a buffer was full, and sign was rotated showing its status.The finished goods area was divided into lanes. Product for a particular customer was segregated into its own lane. Each lane had it's own flip sign as well, showing the status (complete or incomplete) and the customer job number.
An hour-by-hour board was placed at the machine where parts cuts and the hours associated with them were posted, along with the shift goals and job priorities.
Audit
An audit system was put in place to verify compliance with standard work and 5S.
Results
The results were startling. The machine easily beat the customer Takt time of 9.9 minutes, dropping all the way down to 8.1 minutes per part on average. Cut quality and rework also dramatically improved from the better consumables and changeover procedures.
The positive results were not limited to the machine, however. Much like a damn breaking, product flowed now that the constraint had been freed. Downstream departments experienced a surge in efficiency now that they were being fed with enough material. The new customer Takt time had dropped down to 8.3 minutes, which was thankfully still above what the process could supply. Overall the plant efficiency as a whole jumped nearly 15% from the previous levels.
However, a new problem emerged. As always happens when eliminating a constraint via the Theory of Constraints, the next weakest link showed up. The materials group was not getting material in fastest enough to meet the new demand. Systems needed to be revised and new standard work put in place for them as well to help elevate their new constraint.